Predictive maintenance (PdM) leverages different classes of algorithms to predict asset condition, forecast failure, and inform which asset requires attention or a specific intervention by what time. While PdM is not uniquely reserved to artificial intelligence (AI), enhancing established reliability engineering techniques with data-centric models is particularly interesting. They scale well and display a unique capability to distill hidden representations of machine condition and process health from the high-dimensional and multi-modal data created by complex manufacturing machinery.
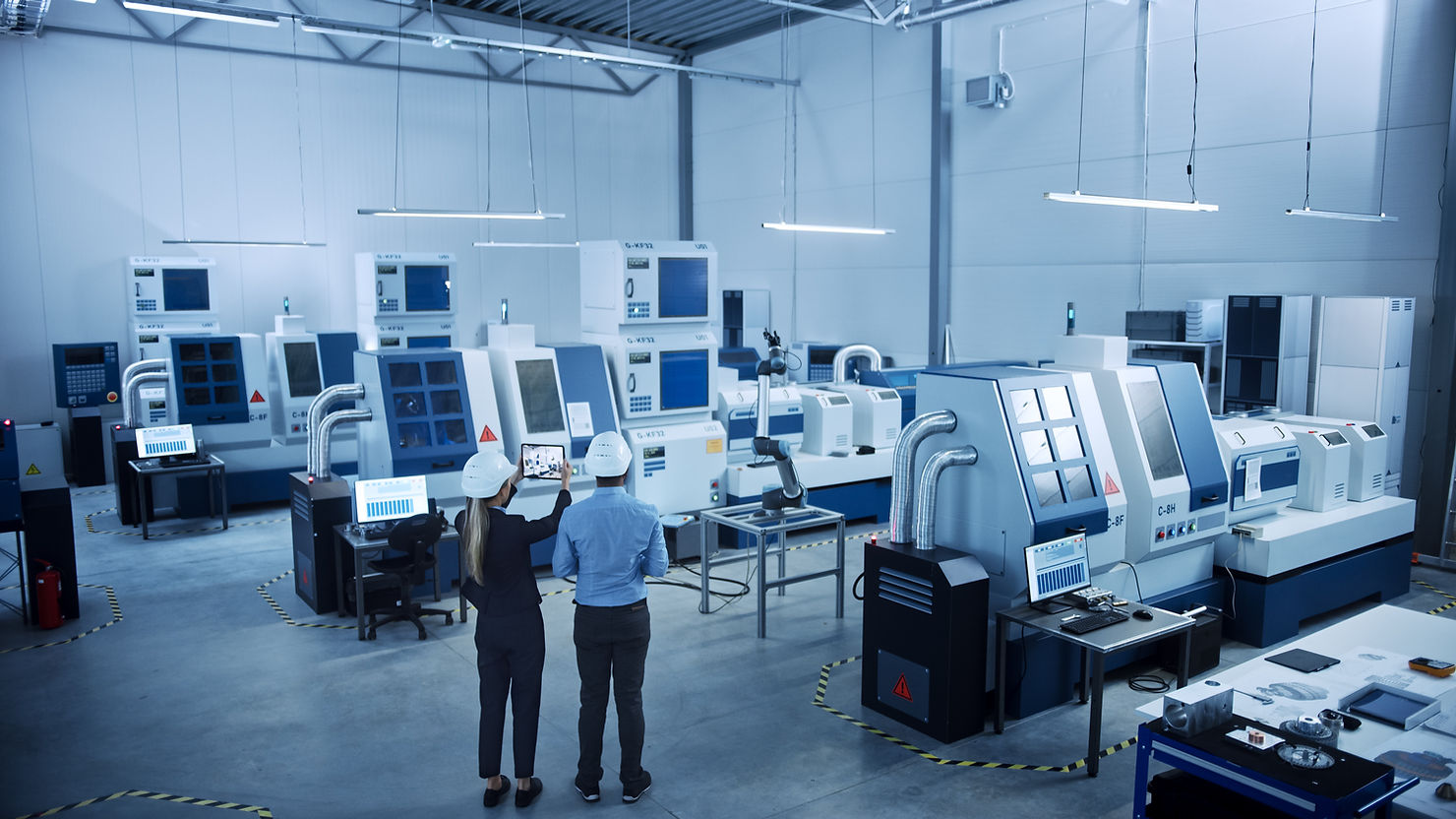
Increased Reliability leads to Cost Reduction
The first opportunity created by PdM is known to many. A purely reactive maintenance strategy reduces asset lifetime at an increased risk of failure resulting to unplanned downtime. According to a 2022 study [1], an average Fortune 500 business loses 11% of its revenues to unplanned downtime. At a macroeconomic level this puts the annual cost of unplanned downtime at 1’500 bn. USD. On the other hand, a scheduled maintenance strategy frequently results in over-maintained assets and is wasteful, both in terms of resources and time.
Numerous examples show how maintenance teams, that follow a proactive strategy, reduce unplanned downtime by 40-80%. They increase their productivity at the same time. The foresight created by predictive maintenance systems is what enables them to be proactive.
PdM Systems provisioned by Machine Manufacturers increase Economic Potential
Commonly, PdM’s cost reduction potential is associated to the machine operator/owner’s perspective. This neglects equally large upstream potentials. Today’s solutions are mostly provisioned by third-party PdM software providers. Simply put, solutions are retrofitted to each piece of equipment on the shopfloor individually.
Machine manufacturers (OEMs) are in a unique position to build technologically more capable systems, that encompass an entire machine population. We are bound to see a paradigm shift once a growing number of them begins to ship their product with the integrated capability to self-monitor, self-diagnose, and even self-correct. OEMs profit from additional value on multiple levels by leveraging the transparency created by a machine population encompassing PdM-system to:
- automate and reduce friction in supply chains and distribution networks for spare parts,
- avoid inventory build-up,
- increase the efficiency of field service operations via remote diagnostics,
- and optimize the planning of field service processes.
Increased Transparency disrupts Value Chains
The lesser known, but broader opportunity lies in PdM’s ability to “disrupt value chains, resize profit pools, and change how economic value accrues to different players” [2]. The trend has been observed in the automotive industry throughout the past decades. It has long become a strategic consideration for executives of machine manufacturers: Economic value is continuously moving downstream in the value chain [2]. PdM allows them to capture more of the value chain:
- the value added for the machine operator/owner by PdM allows OEMs to extend their participation in the servicing of their product throughout its lifecycle,
- the increased operational efficiency enabled by PdM increases OEMs competitiveness in service and spare parts sales at the detriment third parties,
- PdM enables OEMs to create new, increasingly “servitized” business models. The spectrum of opportunities starts with enhanced service contracts up to equipment-as-a-service or pay-per-part business models, which generate stable, recurring revenues at higher profit margins and valuations.
[1] Report: The True Cost of Downtime 2022. Senseye. 2022.
[2] Realizing the Opportunity in Predictive Maintenance Analytics. Ed Maguire, Luca Mazzei, Alberto Cresto and others. Momentum Ventures. 2017.